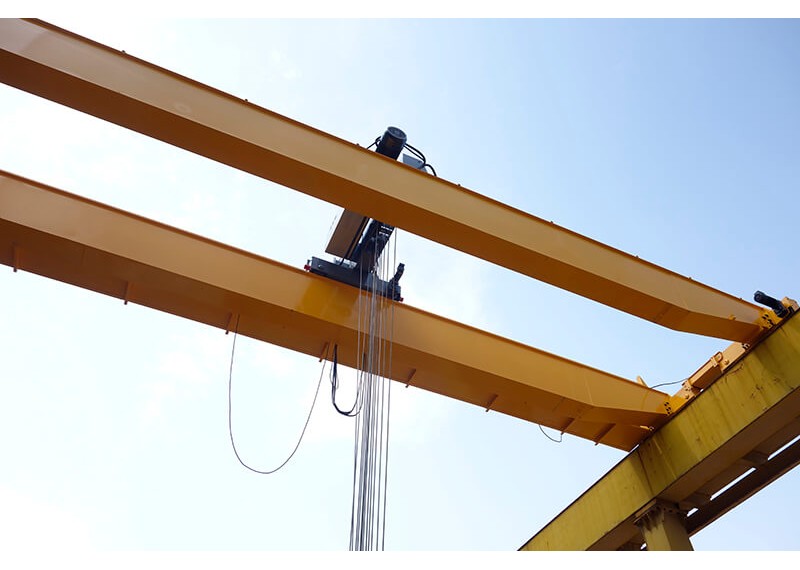
How does the safety problem of the electric single beam crane happen?
Electric Single beam crane has the advantages of simple structure, quick and convenient installation and maintenance, easy operation and easy installation, and relatively cheap installation price. It is widely used in machining, assembly, repair and warehouses and other occasions, and it is more and more favored by small and medium-sized enterprises.
However, there are many problems in its safety. This article makes a simple analysis of the basic evaluation theory of the safety of the crane in terms of the fracture mechanics method and the fatigue strength theory of the Single beam crane.
1. The method of fracture mechanics is a mechanical analysis method for studying the conditions and law of crack propagation in materials, parts and components with cracks. Through fracture mechanics analysis, the allowable size of cracks can be determined, the load-bearing capacity of parts and components can be evaluated, and their service life can be estimated, and the design method of damage tolerance of parts and components can be proposed.
Traditional material mechanics and structural mechanics both assume that the material is a continuum without cracks, and compare the working stress and allowable stress to judge the tension. However, mechanical parts and components, especially large castings and forgings, inevitably have cracks or crack-like defects. Fracture mechanics establishes a quantitative relationship between the dimensions of parts and cracks, loads and mechanical properties of materials, so that the fracture resistance of mechanical parts and components with cracks can be inferred based on the fracture mechanics test data of the samples.
When choosing cast iron or steel in mechanical design, it can be demonstrated with the aid of fracture mechanics analysis. For example, gray cast iron with a tensile limit of only 260 MPa has lower strength than steel, but when used for low-stress cyclic loading, its fatigue resistance is higher than that of mild steel with a similar strength limit. According to the viewpoint of fracture mechanics, the fatigue crack growth rate (cyclic stress, the amount of crack growth caused by each cycle) is related to the magnitude of the stress intensity factor. When this proximity is less than the critical value of the material (called the stress intensity factor amplitude threshold), the fatigue crack does not grow or grows very slowly.
The threshold value of the stress intensity factor amplitude of the gray cast iron is higher than the soft threshold value, so the fatigue resistance is good. The threshold value of ductile iron is often higher than that of general structural steel. However, in the event of overload, mild steel is still better than gray cast iron, so it is necessary to comprehensively consider static strength and fatigue strength.
2. The fatigue strength theory refers to the parts and components that bear cyclic stress. According to the labor intensity theory and the completion experimental data, determine the reasonable structure and size of the mechanical design method. The resistance of mechanical parts and components to fatigue damage is called the fatigue strength of parts and components.
The fatigue strength is determined by the local stress state of the part and the material properties of the part. Therefore, the fatigue design is based on the weakest area of the part. By improving the shape of the part to reduce the peak stress, the surface layer of the weakest area is strengthened. , Can significantly improve its fatigue strength.
Before the fatigue phenomenon of materials is not recognized, mechanical design only considers the static strength, and does not consider the impact of stress changes on the life of the parts. The mechanical products designed in this way often experience fatigue after a certain number of cycles of stress changes after a certain period of operation.
cause brittle fracture to occur suddenly, causing catastrophic accidents, the application of fatigue strength design can ensure the safe operation of the machinery within a given life.
Fatigue strength design methods include conventional fatigue strength design, damage tolerance design and fatigue strength reliability design.