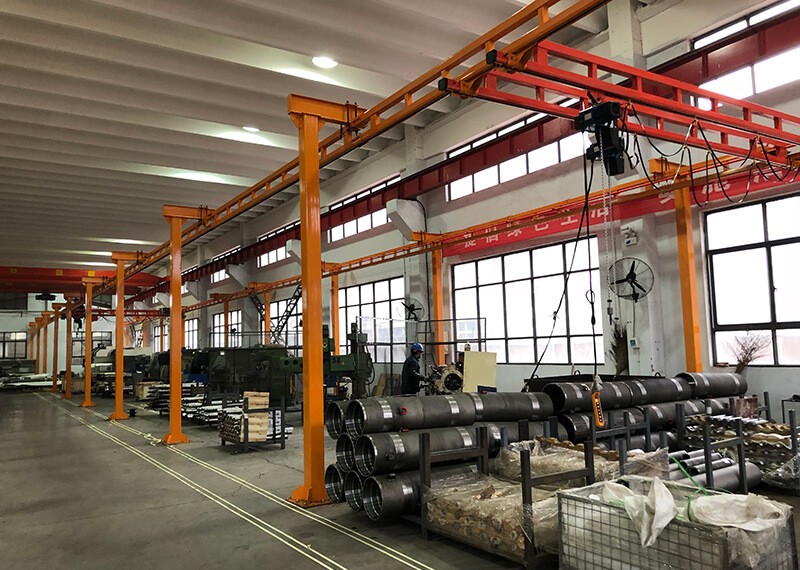
What are the reasons for the power failure of the crane and how to deal with it?
What should we do if we encounter a power failure when using crane? What is the specific reason? Because of inertia, we usually stop the equipment immediately when we use it, so this situation can easily cause the lifting product to be damaged. Unnecessary accidents may occur in serious cases. Today, the editor will give you a brief introduction.
Reason for power failure of crane:
1. The vibration generated during the operation of the cart makes the sliding iron and the guide rail not firmly integrated, and there is a problem with the power supply, which causes the main contact of the main contactor and the normally open auxiliary contact to be disconnected at the same time, and the main contactor coil self-locking fails. Power off.
2. The partial contact of the sliding iron is poor, causing the crane to lose phase instantaneously when it reaches a certain section of the sliding rail. If the missing phase happens to be connected to the control circuit, the coil of the main contactor will be de-energized and self-locking will fail. Even if the device is re-energized after slipping through the poor contact due to inertia, the main contactor coil cannot be closed by itself, and the start button must be pressed again.
3. Vibration generated when lifting heavy objects makes the main contactor not close firmly, the main contact and the normally open auxiliary contact are disconnected due to vibration at the same time, and the main contactor coil self-locking fails and the power is cut off.
Crane power failure treatment measures:
1. The crane control circuit is connected from the three-phase 380V power supply through the switch QS, and the two-phase power supply is taken from the three-phase power supply as the power supply of the control circuit, and the main contactor coil KM is supplied with power, and the overcurrent relay normally closed contact is serially connected in the control circuit. Point KI, KI1, KI2, KI3 to protect each motor from overload.
2. The zero start protection contacts Q1, Q2, and Q3 are connected in series for zero start protection.
3. The safety protection switch SA is connected in series for emergency stop in unexpected situations.
4. Connect 3 limit switches SQ1, SQ2, SQ3 in series for chain protection.
5. The button SB is used to start, and the two normally open auxiliary contacts KM of the main contactor complete the self-locking of the main contactor.
6. The following groups of limit position limit switches and the corresponding two pairs of contacts of each cam controller work together to complete the limit of the crane.
If we find that there is a power outage when we use the crane in our daily use, we should pay attention to it, remove the fault in time, and restore it to normal, so as to ensure that the equipment can exert the ideal use effect.