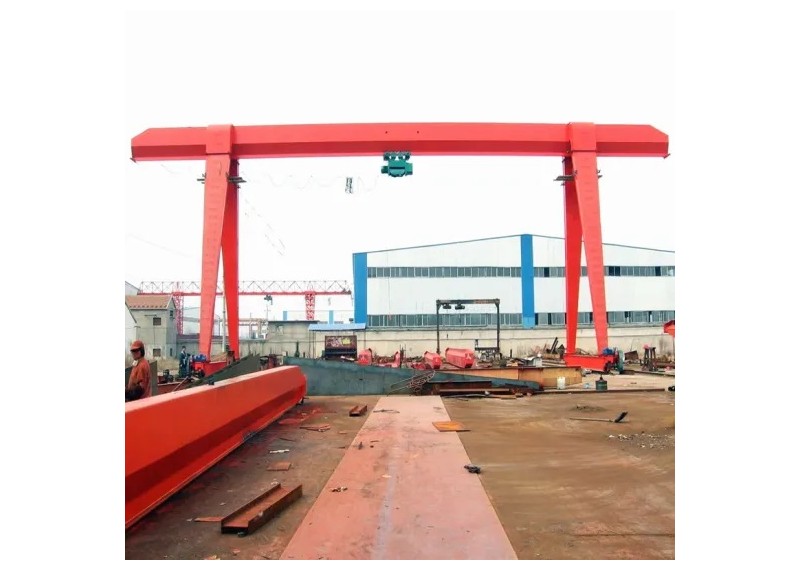
Anti-corrosion experience of metal structure of gantry crane
The damage caused by corrosion of the gantry crane is actually quite amazing. From the rust to the surface, it affects the appearance, and the other is to reduce the capacity of the equipment, shorten the service life, or even scrap it ahead of time. Therefore, good anti-corrosion measures can save a lot of resources.
According to relevant statistics, the metal equipment and materials scrapped due to corrosion every year around the world are equivalent to the metal output of the gantry crane. Because the gantry crane is installed in the open place, its metal structure is exposed to dust and impurities, acid and alkali gases, humid air and hot sun all the year round. Invasion. Due to special working conditions and overloaded operations, metal fatigue and collisions with long and heavy cargo edges destroy the anti-corrosion materials on the surface of the metal structure, and accelerate the formation and spread of corrosion of the metal structure. The parts that often corrode are the outer surface, inner surface, coupling and transmission parts of the main beam that are completely exposed to the air.
At the same time, gantry cranes need to be repaired or overhauled many times from installation and use to scrapping. Mechanical transmission parts and coupling parts can be repaired or replaced, but metal structural parts are hardly replaced. In this sense, metal structural parts are protected. It is even more important.
In order to reduce the corrosion of metal structural parts, it is necessary to understand the causes of metal corrosion and the factors affecting corrosion, so as to prescribe the right medicine, and timely take effective measures to strengthen the protection of the surface of the metal structural parts, so as to improve the life of the metal structure and the whole machine.
At present, the methods used to prevent metal corrosion mainly include: using the steel matrix structure alloying and metal structure single-phase to improve the corrosion resistance of the metal material itself; using the covering method to improve the corrosion resistance of the metal.
Covering method is also called protection method, its essence is to isolate the metal from the external conditions (such as oxygen and water) that can cause corrosion, so as to achieve the purpose of rust prevention. According to the different materials of the protective layer, it can be divided into two types: corrosion-resistant metal covering method and non-metal covering method.
Corrosion-resistant metal covering method is to cover zinc, lead, tin, chromium, nickel, copper and other low-activity corrosion-resistant metals on the surface of the metal to be protected to achieve the purpose of rust prevention.