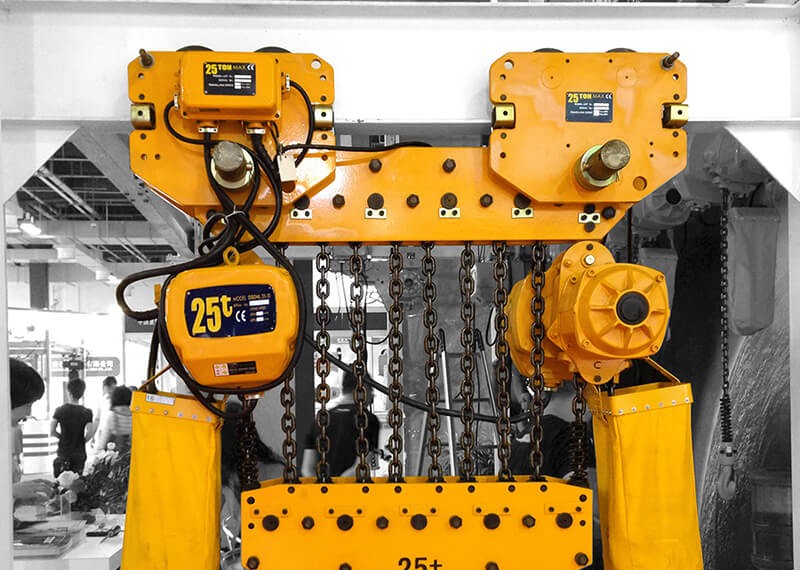
Requirements for the use of electric hoists
The requirements for the use of electric hoists are, first of all, requirements for operators, requiring operators to be at least 18 years old, have good health, hearing, and vision to meet work requirements, and be familiar with equipment performance and operating procedures. The electric hoist should be checked daily before each shift. There are no abnormalities in the wire rope, hook, brake, flashlight door, lubrication and the work site, and no disease operation is allowed.
In addition, the requirements of the operator in the operation are the most important. It is forbidden to overload the use, and it is forbidden to lift buried objects and objects with unclear weight. It is forbidden to pull diagonally to prevent damage to the rope guide and wire rope. The lifting limiter is a safety device designed to prevent the hook from rising or falling beyond the position and causing an accident. It cannot be used as a normal stop switch to prevent accidents caused by malfunction. Do not adjust the brake while lifting heavy objects. When hoisting, people are not allowed to pass above people; when the heavy objects are still in the air, people are not allowed to enter under the heavy objects. After the work is completed, the main power supply must be cut off, and heavy objects are not allowed to hover in the air to prevent deformation of the machine parts.
The noise generated by the mechanical friction of the electric hoist is mainly caused by the mechanical failure of the motor, mainly due to the friction between the stator and the rotor, the bearing oil leakage, and the bearing overheating. Stator and rotor rubbing: Because the gap between the stator and the rotor is very small, often due to the uneven air gap, the iron filings, burrs, and paint film in the motor are not cleaned, not only increase the noise and vibration, but also significantly increase the iron core. Local overheating and winding insulation damage should be dismantled, inspected and dealt with in time. Bearing oil leakage, bearing overheating: It is mainly caused by too much or too little bearing grease, unclean grease, poor bearing quality and many other reasons. You will hear a "squeak-squeak-" sound during operation. The bearing should be removed and washed in time And observe the surface of the raceway, check that the relevant dimensions are in line, and then take measures. In addition to the mechanical failure of the motor, it is also necessary to check whether the coupling connected to the reducer rotates and whether the concentricity meets the requirements. Factors such as uneven installation foundation, bent shaft extension, and unbalanced transmission unit will cause abnormal noise and corresponding vibration. The user must use the sound he hears to judge the fault caused by the motor and solve it in time.