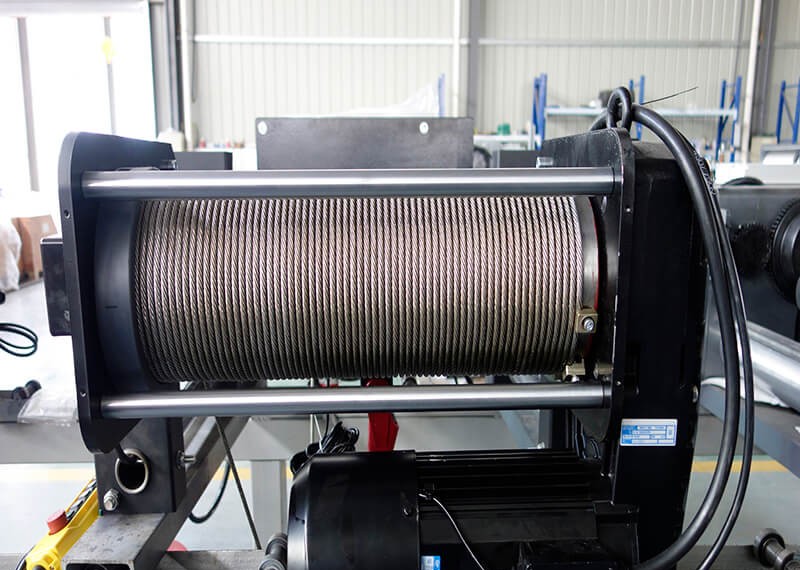
Introduction of anti-corrosion measures for wire rope
Wire rope anti-corrosion: There are two anti-corrosion measures: oiling and plating.
Oiling: All steel wire ropes must be oiled. The fiber core is immersed in oil, and the grease is required to protect the fiber core from decay and corrosion of the steel wire, moisturize the fiber, and lubricate the steel wire rope from the inside. The surface is coated with oil so that all the steel wires in the strands are evenly coated with a layer of anti-rust lubricating grease. For mine ropes with increased friction and large mineral water, black oil grease with strong abrasion and water resistance should be coated; other uses It is coated with red oil grease with strong film-forming properties and good rust resistance, and requires a thin oil layer, which is convenient for keeping clean during operation.
Coating: galvanized, aluminized, coated with nylon or plastic, etc. Galvanizing is divided into thin coatings of steel wire first and then drawn and thick coatings of galvanized steel after drawing. The mechanical properties of thick coatings are lower than that of smooth steel wire ropes, so they are suitable for use in severely corrosive environments. Aluminum-plated steel wire rope is more corrosion-resistant, wear-resistant and heat-resistant than galvanized steel wire rope. It is mainly used in fishing trawlers and mines containing H2S. It is produced by the method of first plating and then drawing. The steel wire rope coated with nylon or plastic is divided into two types: coated rope and coated stranded rope. The former is used for static cables, and the latter is used for moving cables.