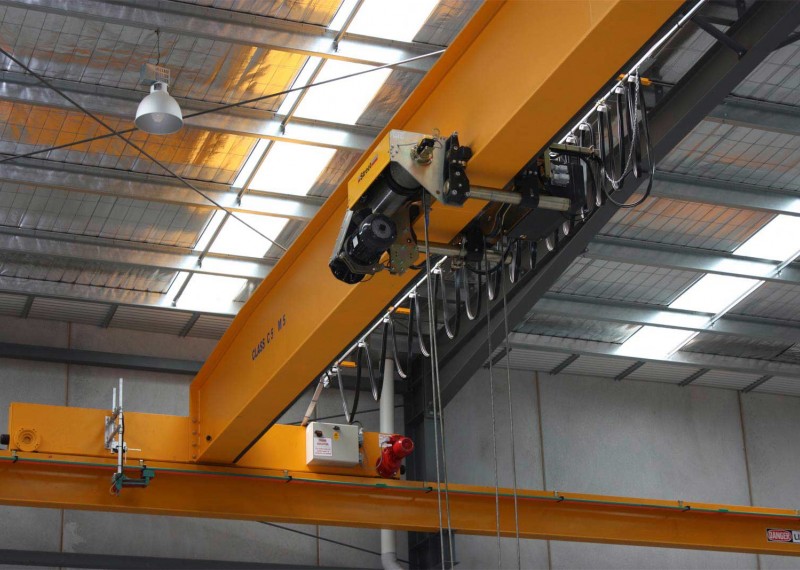
Electric overhead crane operation
Five rules for operation of electric overhead crane
1. Implement fixed person and machine, operate equipment with operation certificate;
2. Always keep the equipment clean and tidy, add (change) oil according to regulations to ensure reasonable lubrication;
3. Comply with safe operation procedures and shift system;
4. Take good care of the accessories and tools of the equipment without damage or loss;
5. If any abnormality is found, stop the vehicle immediately for inspection. If it cannot be handled by itself, inform relevant personnel in time for inspection and treatment.
What are the hazards in the operation of electric overhead crane
Electrical Hazards
According to OSHA, nearly 50 percent of overhead crane accidents are the result of machinery coming into contact with a power source during operation. Power line contact is literally defined as the inadvertent contact of any metal part of a crane with a high-voltage power line. Power line contact most often occurs when the crane is moving materials nearby or under energized power lines and the hoist line or boom touches one of them. Usually, the person who is electrocuted is touching the crane when it comes into contact with the power line. But, the danger is not just limited to the operator. It extends to all personnel in the vicinity.
Overloading
According to OSHA, 80 percent of all crane upsets and structural failures can be attributed to exceeding the crane’s operational capacity. When a crane is overloaded, it is subject to structural stresses that may cause irreversible damage. Swinging or sudden dropping of the load, using defective components, hoisting a load beyond capacity, dragging a load and side-loading a boom can all cause overloading.
OSHA estimates that one crane upset occurs for every 10,000 hours of crane use. Nearly 80 percent of these upsets can be attributed to predictable human error when the operator inadvertently exceeds the crane’s lifting capacity. Overloading most often occurs when poorly trained personnel are allowed to operate cranes. Oftentimes, operators mistakenly believe they are able to rely on their instinct or experience to determine whether a load is too heavy. It’s crucial that any crane operator know the weight of a load and the capacity of the crane. Using technologies such as load-measuring systems for training and planning can greatly reduce the hazard of overloading and operator incompetency.
Materials Falling
Falling materials is a major concern at any work place or job site using overhead cranes. Visual impairment, two-blocking, slipping, mechanical failure, or operator incompetency can all result in serious injuries or fatalities. If materials are not properly secured, for instance, the load can slip and land on workers in the vicinity or cause major damage to property. For larger or mobile cranes, undesired movement of material can pinch or crush workers involved in the rigging process.
Statistics show that nearly 20 people died in 2012 as a result of accidents with overhead hoists. That’s because the loads being lifted by overhead hoists tend to be fairly heavy and cause serious damage if dropped. Slings and attachments that aren’t secured properly can be a major safety hazard, and when objects begin to slip, they will eventually crash to the floor below.
One way to reduce the risk of falling materials is to perform regular maintenance of hoists. Load testing maintenance ensures that you know how many pounds the hoist can handle, and it helps to maintain good working condition. Maintenance should always be treated seriously when it comes to heavy machinery. If a moving part on an overhead crane wears out or breaks the hoist, it can cause serious damage. Performing regular maintenance ensures the hoist and overhead crane remain in good working order and that all operations run smoothly.