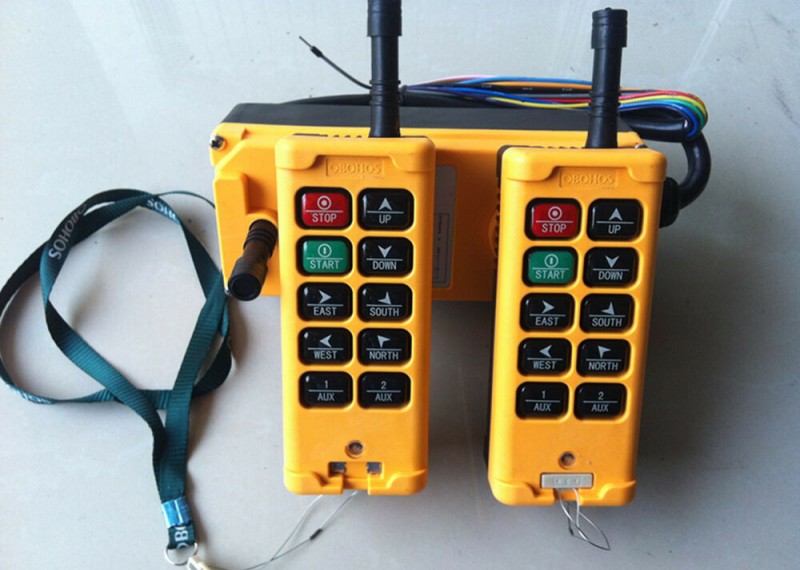
Overhead Crane Controls: Push Button Pendants vs. Radio Controls
On electrified overhead crane systems, the crane’s controls allow an operator to direct the movement of the crane and the hoist. The three types of movement that are influenced by a crane’s control system are:
Crane motion – moving the crane up and down the runway(s)
Hoist positioning – side-to-side / lateral movement
Hoist lifting motion – moving the hook up and down
There are two ways that a crane can be operated:
An operator can control the crane from an exposed or enclosed cab attached to the crane and utilize one or two other co-workers on the ground who help guide and position the load using hand signals.
A crane can be controlled by an operator on the floor using a push button pendant system that is attached to the crane itself, or a wireless control that utilizes a radio transmitter and receiver.
Over time, there has been a trend towards moving operators out of the cabs and putting them down on the floor where they’re closer to the load—giving the operator increased visibility and better vantage points to lift and lower loads.
With pendant or radio controls, you can operate a crane to lift, position, and lower the load with one person. For years, the standard crane went out with pendant controls, but over time the prices of radio controls have dropped—evening out the cost of both types of control systems.
If a crane operator is trained properly, pendant and radio controls can both be perfectly safe methods for controlling and operating a crane. However, when researching and designing an overhead crane system, our customers frequently ask us whether push button pendant controls or radio controls are better, or which system they might be able to use to upgrade or modernize their overhead crane.
In this article, we’ll compare these two types of overhead crane controls and provide an explanation of how both work, as well as the advantages and disadvantages of both types of systems.
Radio Controls for Overhead Cranes
A wireless remote transmitter with a series of buttons or levers is either held by the operator or is clipped onto a harness or belt worn by the operator. The remote transmitter sends a radio signal to a receiver unit mounted on the crane. This unit transforms the signal into electrical energy and passes it on to the intermediate relay unit on the crane, and the appropriate contact is activated to then move the crane up and down the runway, move the hoist or trolley side to side, and raise or lower the hook.
Advantages of Using Radio Controls
20-30 years ago, radio controls for an overhead crane system had a pretty bad reputation. They were expensive and also experienced a lot of interference issues that caused control problems—ultimately leading to productivity issues and frustration for the end-user.
Over time, advances in technology have greatly improved the functionality of the transmitter and receiver—becoming a solid and reliable choice for controlling an overhead crane system. Also, as wireless and radio control technologies became more prevalent, the price of these remote systems has reduced drastically—making them more of a cost-effective solution and more in line with the cost of pendant control systems.
Radio controls are battery-operated and can be handheld or designed in a “bellybox” style, where the operator clips it onto their belt or attaches it to a harness or shoulder strap. Both styles can be compact, lightweight, and ergonomically-designed—with multiple speed configurations and intuitive controls.
The main advantage of using a radio control for your overhead crane is that it eliminates the dependence on being tethered to the crane itself—either via cab controls or pendant controls. Because the operator doesn’t have to be near the load to lift, position, or lower it, radio controls can help protect them from hazards like:
Vapor, smoke, or chemical exposure
Radiation
High heat or hot metals
High voltage / electric shock
High humidity
Not only can the operator work on the floor safely away from hazards, but they’ll also get a better vantage point to perform the lifts effectively. The operator doesn’t necessarily have to walk with the load as it moves down the crane bay, so radio controls help keep the operator away from trip or fall hazards like obstacles on the floor, workers, and other machinery or equipment in operation. They’re also ideal for higher duty classes like D, E, or F where the crane runs up and down the runways more often, and at a faster rate.
A cost-savings benefit of operating a crane via radio controls is that it offers improved visibility for the operator. With only one operator required to control the crane from the ground, you no longer need a team of two or three workers operating a crane from cab and the floor to lift, move, and lower loads via hand signals. Productivity can also be improved with better visibility–helping with faster load positioning and damage control as the operator can better judge load and clearance obstacles from the ground.
Advanced engineered radio controls can also provide diagnostics and data information to the crane operator or to a service technician who is on site servicing or inspecting an overhead crane. These advanced radio systems can supply data on:
Runtime usage
Drives
Weight on the hook
Number of picks or hooks made
Diagnostics or fault codes for issues requiring maintenance
In the event of an issue or fault code that requires maintenance, a crane service technician can pull information right off of the radio control rather than having to get up on a lift to dig around and find the cause of the problem.
Disadvantages of Using Radio Controls
Radio crane controls are not recommended for Class A or Class B type cranes that don’t get used very often. The reason being that the controls are battery operated and there’s an increased chance that the batteries will be dead or won’t be charged fully when the crane needs to be operated.
Again, because these controls run off of replaceable or rechargeable batteries, radio controls need to have the batteries checked or replaced often, which can cause headaches for the operator and affect production if not maintained properly.
Another disadvantage to using a radio control for controlling an overhead crane is that it is more susceptible to damage because it’s a handheld device. Although it’s made of sturdy plastic and rubber materials, it can still sustain damage that may affect functionality if dropped repeatedly.
Although not very common, there are environments that create their own radio waves that may interfere with the operation of an overhead crane. An example might be a facility that performs induction heating or induction welding procedures. Radio waves created during these processes may disrupt the communication between the radio’s transmitter and receiver.
Finally, because the the transmitter is not tethered to the crane, it can be misplaced if a central storage location is not pre-determined.
Pendant Controls for Overhead Cranes
A handheld controller with push buttons is directly wired into the hoist or a separate festoon track and hangs down to be used by the operator. The operator holds the control pendant and walks with the crane and the load as he moves it down the runway. The operator can also laterally position the hoist and control the up and down lifting movement of the hook using the pendant control.
Advantages of Using Pendant Controls
Years ago, pendant controls used to go out with just about all types of overhead crane systems. As the prices of radio control systems dropped, they became more widely-used. Pendant systems are still very popular today because of their reliability and ergonomic design changes to make them more comfortable for the operator to use. Today’s pendant design is a much smaller and lighter piece and can be operated using one hand.
The most important advantage that pendant controls have is their reliability. Because they’re hard wired into the hoist or a festoon system, there is no interference between a remote radio transmitter and the receiver.
Due to their rugged design, pendant controls are highly resistant to mechanical damage and contaminants. Some of the benefits of their design include:
High impact resistance – can’t be dropped by the operator, since it’s suspended from the crane
Resistance to corrosion, moisture, dust, dirt, and grime
Insulated design provides shock resistance
Ergonomic design for comfort and less fatigue for the operator
Although pendant controls can be used on almost any type of overhead crane, they are ideal for cranes that are in lower duty cycle classes. Because it is hardwired into the electrification system, the crane controls will always have power, so the operator doesn’t have to worry about replacing or charging batteries for a crane that doesn’t get used too often. Often, pendant controls are the preferred control method for explosion proof cranes.
Compared to radio controls, the pendant is always readily available since it hangs down from the crane itself. The operator doesn’t have to worry about finding it or keeping track of it like they would with a radio transmitter.
Disadvantages of Using Pendant Controls
The major disadvantage of using a pendant control is that it puts the operator close to the load at all times. Especially when working with heavy loads and/or hazardous materials like hot metals or chemicals, putting the operator near the load can increase the chance of an accident or exposure to harmful materials.
Another major disadvantage is that the operator has to follow the load along the floor of the facility, and this can increase the risk of a trip or fall hazard. The operator has to be aware of material or obstacles on the floor and also know where their co-workers are working and what machinery or equipment is operating nearby.
Overhead cranes that are in high-use duty cycles, can move up and down the runway quickly and it can be difficult or impossible for the operator to keep up using a pendant system. In situations where a process crane or a Class D, E, or F crane are being used, it’s much more practical for the operator to control the crane from a cab or by using a radio control.
Finally, the pushbutton controls can get caught on machines or other obstructions within a crane bay, which can cause the pendant to become disconnected from the crane. In addition, the wires inside the pushbutton cable can break over time due to pulling and catching on obstructions and obstacles as it moves down the crane bay.
As long as your crane operators have been properly trained, both pendant controls and radio controls are good options for safely controlling the movement of the crane and hoist.
While pendant controls were the standard for many years, radio controls have become more reliable and the price has decreased so now they’re more common on standard crane systems. However, the ruggedness and reliability of a pendant control continues to make it a popular choice when designing crane systems for our customers.
At Dongqi, we have relationships with the leading crane control manufacturers in the industry. We offer all kinds of pendant and radio controls from basic configurations, to multi-speed controls, and engineered systems with customized controls and diagnostics.
If you’re interested in pricing out a new overhead crane system, or want to upgrade or modernize the controls on your existing overhead crane system, contact us today to speak with a crane specialist.