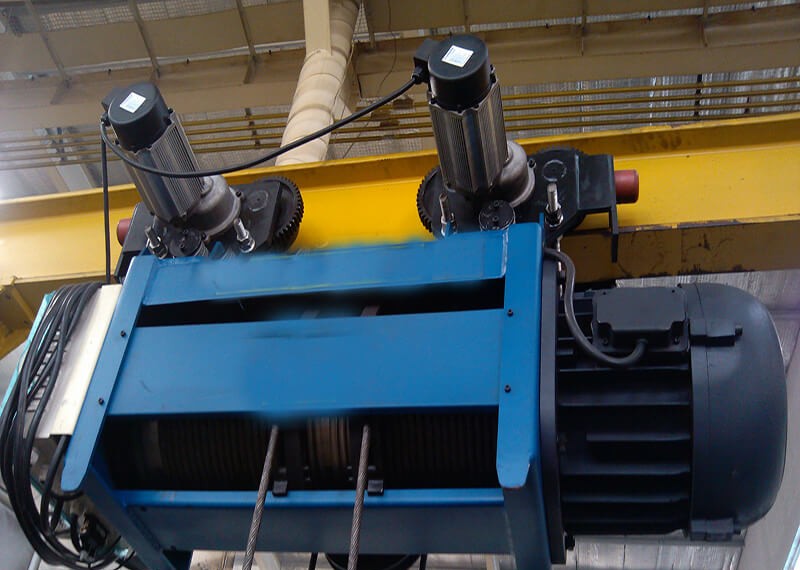
Method for preventing corrosion damage of steel wire rope
Wire ropes are generally used in the open air. Sun and rain will corrode the wire ropes, especially the wire ropes used in harmful gases and harsh environments, the damage caused by corrosion will be more serious. There is a difference in oxygen affinity on the surface of the steel wire rope damaged by corrosion, so that a certain part of the surface metal becomes the anode, and another adjacent part of the metal becomes the cathode, forming a large number of small batteries. Under the action of the small battery, many circular corrosion pits are formed on the surface and gradually deepen. These pits become stress concentration points and the source of fatigue cracks. At the same time, corrosion reduces the cross-sectional area of the wire rope, and reduces its elasticity and ability to withstand impact.
There are two ways to prevent the corrosion and damage of the steel wire rope. One is to apply oil frequently, which is indispensable for the steel wire rope that is often in motion. New steel wire rope hemp core generally contains 12% to 15% grease, while scrap steel wire rope only contains 2.4% grease in the part with the greatest loss. At the end of the same steel wire rope, even if it does not pass through the pulley, it still contains 12.7% to 14.5%. Of grease. The test shows that the breakage of the oil-coated steel wire rope in the later stage of the test is about half of that of the non-oil-coated wire rope. The initial oil content of a steel wire rope can only maintain 40% of its life. If no oil is added thereafter, the wire breakage will increase sharply. Second, special steel wire ropes such as galvanized and aluminum-plated can be selected for steel wire ropes with harsh environment and less relative movement. The galvanized or aluminum-plated surface of these steel wire ropes exposed to the atmosphere will form a thin film of zinc hydroxide and aluminum hydroxide, which can effectively prevent corrosion of the steel wire rope.