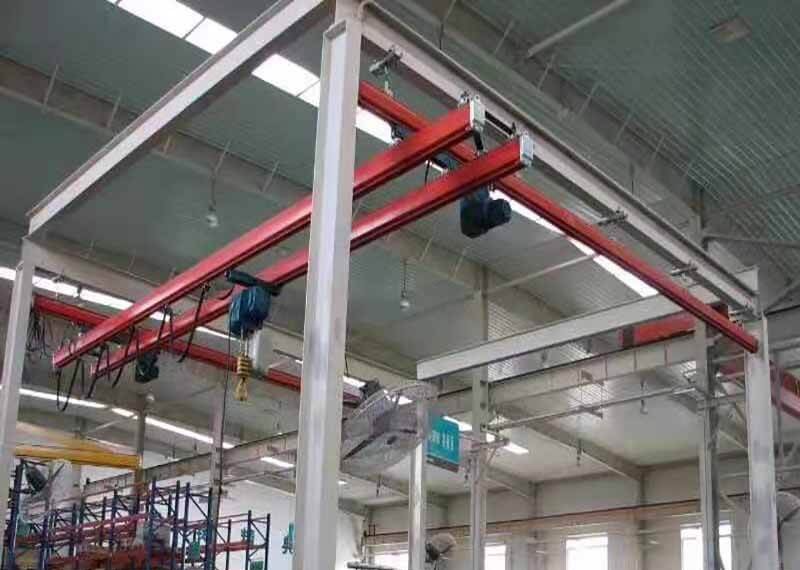
How to avoid the wear of crane components
To extend the service life of the crane, the basic thing is to reduce the grinding of parts. So we first understand the causes of component wear. There are different preventive measures for different causes of crane wear. Friction and wear can be solved by adding lubricating oil and removing impurity particles at the friction part. However, if the wear is caused by corrosion, the correct method should start from the replacement of materials, and try to use unstable chemical or electrochemical reaction crane parts to avoid the influence of wear.
Regarding the crane wear caused by corrosion, the correct method should start with the replacement of materials, and try to use crane accessories with unstable chemical or electrochemical responses to achieve anti-wear effects. Regarding the corrosion of the appearance of the equipment, anti-corrosion coatings can be sprayed to avoid contact of the metal surface with air.
Affected by the processing, assembly, and adjustment of new parts, the crane has a rough conflict surface, a small touch area on the cooperation surface, and uneven surface pressure. During the working process of the machine, the concave and convex parts of the surface of the parts are inlaid and conflicted with each other, and the metal scraps ground by the abrasive tools continue to participate in the conflict, which accelerates the wear of the cooperative surface of the parts. Therefore, during the running-in process, the wear of the parts is simply caused, and the wear rate is fast. At this moment, if overloaded work, it may cause damage to the crane parts and early failure.
Due to its outstanding functions and selectivity, cranes are widely used in various industries and have achieved outstanding effects. However, the crane also has all mechanical equipment failures, and the wear and tear of parts will directly affect the service life of the equipment. We should try our best to reduce the wear of parts. This can extend the service life.