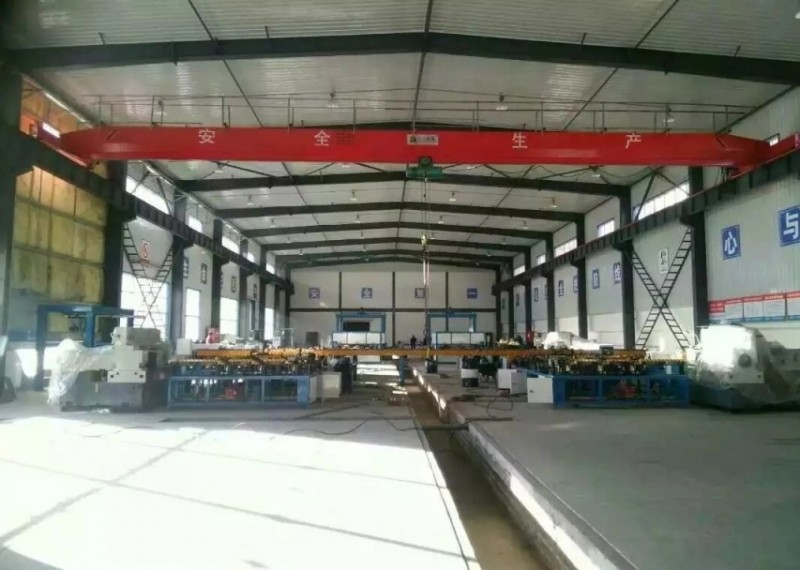
Electric single beam crane inspection items and requirements report
When the electric single-beam crane is inspected, the contents must comply with relevant regulations. The editor introduces the inspection content and requirement report form of the electric single-beam crane for your reference.
Report form:
Test items | Serial number | Inspection content and requirements | Test results | in conclusion | |
Safety and health | 1 | The equipped electric hoist should be equipped with safety devices and take safety measures in accordance with the provisions of JB/T9008.1 or JB/T5317. | Meet the requirements | qualified | |
2 | The operating mechanism of the crane trolley should be equipped with an operating limit position limiter and its action should be reliable. The crane and trolley should be equipped with buffers and comply with the requirements of JB/T8110.2 and JB/T10833. | Meet the requirements | qualified | ||
3 | The crane should be set with overload limiter according to GB6067 . | Meet the requirements | qualified | ||
4 | The crane shall be equipped with protective measures such as emergency stop switch, short circuit protection, and voltage loss protection. Low-voltage control (not greater than 50V) should be used when electric door operation is used, and zero protection and interlock protection should be set when operation in the driver’s cab. | Meet the requirements | qualified | ||
5 | After the power is turned on, ensure that the direction of movement of the crane and electric hoist is consistent with the button mark. | Meet the requirements | qualified | ||
6 | The insulation resistance value of the crane at room temperature should not be less than 1MΩ. | ||||
7 | The grounding resistance of the crane should not be greater than 4Ω. | ||||
8 | The crane should be equipped with a normally closed brake. | Meet the requirements | qualified | ||
9 | The sound pressure level noise of the complete crane should not be greater than 85dB(A). | ||||
10 | The headroom height of the driver’s cab should not be less than 1.8m, and the height of the fence of the driver’s cab should not be less than 1000mm. | No item | No item | ||
11 | The driver’s cab should be equipped with a fire extinguisher and an electric bell or alarm. | ||||
12 | The door into the crane and the door from the driver’s cab to the bridge frame should be equipped with electrical interlocking protection devices. When any door is opened, all the crane mechanisms should not work. | No item | No item | ||
13 | The safety dimensions of the crane should meet the requirements of Table 1 (see Figure 1 to Figure 3)![]() | ||||
Test items | Order No. | Testing content and requirements | Test results | in conclusion | |
Material quality | 14 | The material of the crane metal structure, carbon structural steel according to GB700, and low-alloy structural steel according to GB1591, the selection of grades should meet or not be lower than the regulations. | Meet the requirements | qualified | |
15 | The wheel of the trolley is made of 45 steel with performance not lower than GB699 and quenched and tempered. | Meet the requirements | qualified | ||
16 | The quality of the metal material should have the qualification certificate of the supplier, otherwise the manufacturer should do chemical analysis and mechanical performance test. | Meet the requirements | qualified | ||
Main parts | 17 | The wheel tread diameter tolerance is h9, measured with an outside micrometer. | Meet the requirements | qualified | |
18 | The wheel tread hardness is 300~380HB. | Meet the requirements | qualified | ||
19 | After the wheel is installed, its reference end surface should be on the inner side of the crane, and the end surface circle runout is specified as follows, diameter ≤ 250mm, not more than 100μm;> 350~500 not more than 120μm. | Meet the requirements | qualified | ||
20 | The accuracy of the reducer and gear pair used in the operating mechanism is not less than 8-8-7, and the open gear is not less than 9-8-8. | Meet the requirements | qualified | ||
twenty one | The performance of the matching motor shall not be lower than the regulations of JB/T9008.6-1999. | Meet the requirements | qualified | ||
twenty two | The wire rope electric hoist for the hoisting mechanism shall comply with the regulations of JB/T9008.6-1999. | Meet the requirements | qualified | ||
Welding quality | twenty three | Weld appearance quality requirements: There should be no visible defects on the outside of the weld. According to GB6417, these defects are classified as: cracks, holes, solid slag inclusions, lack of fusion, incomplete penetration, shape defects and other defects other than the above. | Meet the requirements | qualified | |
twenty four | The butt-welded joint welds of the main stressed structural parts comply with the design regulations. The butt welds of the tension zone of the main beam and the spreader beam shall be subjected to 100% radiographic or ultrasonic inspection; radiographic inspection shall be in accordance with GB/T3323-2005 The requirements of Radiography for metal Fusion Welding Joints, the transillumination technology is not less than A, and the qualified level is Ⅱ; Ultrasonic wave testing is in accordance with the requirements of JB/T10559-2006 “Crane Nondestructive Testing of Steel Welding and Overbearing Testing”, in accordance with the requirements of Level 1. Welding grid requirements for evaluation. | Meet the requirements | qualified | ||
Bridge ( crane running machine mechanism assembly accomplished in rear) | 25 | Local warpage of the web of the main beam: when the height of the web is not greater than 700mm, check with a 500mm flat ruler, the compression area of the web (within H/3) should not be greater than 3.5mm, and the tension area of the web (H/ 3) should not be greater than 5mm; when the height of the web is greater than 700mm, check with a 1000mm flat ruler, the compression area of the web (within H/3) should not be greater than 5.5mm, and the tension area of the web (beyond H/3) ) Should not be greater than 8mm. | Meet the requirements | qualified | |
Test items | Serial number | Inspection content and requirements | Test results | result | |||
Bridge ( crane running machine mechanism assembly accomplished in rear) | 26 | The base distance W is (1/8~1/5)S, but generally not less than S/6. | Meet the requirements | qualified | |||
27 | The maximum camber of the main beam should be within the S/10 range of the mid-span (see Figure 4). Before the static load test, the recommended value of the upper arch F of the main beam is (1/1000~1.4/1000)S. | Meet the requirements | qualified | ||||
28 | The horizontal bending value f of the main beam should not be greater than S/2000, and this value is measured at a point 100mm from the top surface of the main beam on the web. For cranes equipped with angular trolleys, only concave bending to the side of the main track is allowed (see Figure 4). | Meet the requirements | qualified | ||||
29 | After the crane operating mechanism is assembled, measure the limit deviation of the crane span △S: when S is not greater than 10m, it is ±2 mm, when S is greater than 10m, △S=±[2+0.1(S-10)]mm. | Meet the requirements | qualified | ||||
30 | The diagonal difference measured at the reference point of the wheel mounted │E 1 -E 2 │ is not more than 5mm (see Figure 4). This value allows control before the assembly of the operating mechanism. | Meet the requirements | qualified | ||||
31 | base distance deviation △W, when W is not greater than 3m, △W is ±3; when W is greater than 3m, △W is ±W/1000. | Meet the requirements | qualified | ||||
assembly | 32 | After the crane is assembled, the vertical deflection of the wheels should be controlled within the following range: 0.0005≤tanα≤0.0030 (see Figure 5). | Meet the requirements | qualified | |||
33 | After the crane is assembled, the horizontal deflection of the wheel axis is tanφ=﹣0.0020~﹢0.0020. | Meet the requirements | qualified | ||||
34 | After the crane is assembled, the height difference △h of the four wheels should meet the requirements of Table 3. table 3 | ||||||
Span S m | Limit deviation△h mm | ||||||
≤10 | ±2 | ||||||
>10~15 | ±3 | ||||||
>15~20 | ±4 | ||||||
>20~25 | ±5 | ||||||
>25~31.5 | ±6 | ||||||
Test items | Serial number | Inspection content and requirements | Test results | in conclusion |
Steel pretreatment inspection | 35 | Crane metal structure should be treated with a rust steel surface, an important member of GB8923 quality should Sa2 in 1 / 2 level or St3 level, should reach the other portions, or St3 level Sa2 level. | Meet the requirements | qualified |
36 | The crane paint shall be uniform, bright, complete and consistent in color, and shall not have defects such as roughness, paint leakage, wrinkles, pinholes and sagging. | Meet the requirements | qualified | |
37 | The thickness of the paint film of the topcoat is 25~35μm per layer, and the total thickness is 75~105μm. | Meet the requirements | qualified | |
38 | The paint film adhesion of the main stressed components should meet the quality requirements of Grade 1 in GB9286. | Meet the requirements | qualified | |
39 | Before the crane leaves the factory, anti-rust measures should be taken on all exposed processed surfaces. | Meet the requirements | qualified | |
Electrical Equipment | 40 | The technical performance of the electric control equipment, stopper and other electrical parts and components of the electric hoist shall meet the corresponding requirements of JB/9008.1 or JB/T5317. | Meet the requirements | qualified |
41 | Crane feeder can use trolley wire or cable. When angle steel trolley wire is used, protection device should be provided. When there is a driver’s cab, the sliding line and the driver’s cab should generally be arranged at both ends of the crane’s main beam. It is recommended that the sliding contact line adopt the sliding connection transmission device conforming to JB/T6391.1. | Meet the requirements | qualified | |
42 | The wires to be laid in the protective line pipe and the wires to be laid in the control box and the driver’s compartment should all be copper-core multi-strand wires. The cross-sectional area of the main circuit conductor is selected according to the controlled power and shall not be less than 1.5mm 2 . | Meet the requirements | qualified | |
43 | The wire protection tube shall be firmly fixed on the bridge frame, the nozzle shall be equipped with a wire protection nozzle, and the wires laid in the wire protection tube shall not have any joints. | Meet the requirements | qualified | |
44 | The metal shells of all electrical equipment on the crane must be effectively grounded. | Meet the requirements | qualified | |
45 | The insulation resistance value of each circuit in the electric control equipment of the crane shall meet the requirement of “The insulation resistance value of the crane at room temperature shall not be less than 1MΩ”. | Meet the requirements | qualified | |
46 | Electric hoist operation adopts cable or slip connection power transmission device to feed power. The steel wire rope used for erecting the mobile cable should be galvanized, and the pulley and pulley track should be derusted and painted or galvanized. | Meet the requirements | qualified | |
47 | The electric control equipment of the crane except for the electric hoist shall meet the corresponding requirements of JB/T4315. | Meet the requirements | qualified | |
48 | When the crane adopts remote control operation, it shall comply with the regulations of JB/T8437. | Meet the requirements | qualified |
Test items | Serial number | Inspection content and requirements | Test results | in conclusion |
experiment method | 49 | The crane test should follow the specifications and procedures specified in GB/T5905. | Meet the requirements | qualified |
50 | Visual inspection: The content of the visual inspection should include whether the specifications and status of all important components meet the requirements, such as: various mechanisms, electrical equipment, safety devices, signal systems, metal structures and their connections, all protective devices, electric hoists and accessories And so on, the necessary certificates and other documents should also be checked. During inspection, it is not necessary to disassemble any parts, but the cover that should be opened during normal maintenance and inspection should be opened. | Meet the requirements | qualified | |
51 | No-load test: turn on the power supply, start the various mechanisms, make the trolley run along the full length of the main beam, check whether there is jamming, start and check other mechanisms, check whether the operation is normal, whether the control system and safety devices meet the requirements and are sensitive and accurate , Check the lifting height and hook limit position. The cumulative time of the experiment is not less than 5 minutes. | Meet the requirements | qualified |
Note:
1. This report is applicable to electric single-beam cranes.
2. When filling in the report, if there are data for inspection and testing, the actual measured data should be filled in.
3. This report is in triplicate, and one copy is kept by the company’s quality inspection department, the user and the local labor safety supervision agency.