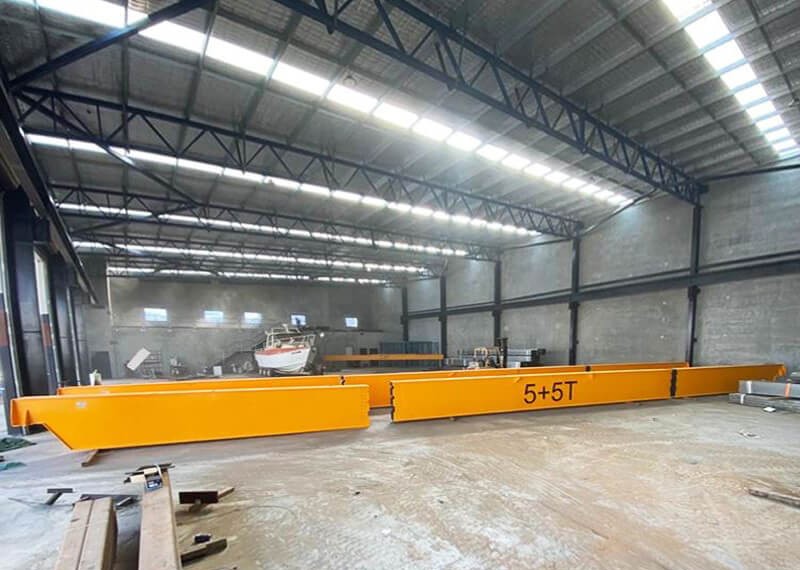
Welding requirements for crane rail joints
The running rails of cranes are generally relatively long, and multiple rails need to be welded together. In order to ensure the safety of the track, there are certain requirements for the track welding.
1. Preparation before welding
Before welding the crane rail joint, carefully clean the groove and nearby oil, rust and other dirt until the metallic luster is exposed. The welding material is matched with the basic electrode according to the principle of equal strength, and its grade is J857 (national standard
2. Control of orbital welding deformation
The pre-padded height of the rail end is determined by the type, length and fixation of the rail, as well as the environmental temperature and other factors. The rail end is pre-padded with copper backing plate and carbon steel plate by 30-40mm. Connecting parts such as bolts and pressure plates, tighten the nuts to fix the rails on the rail beams, and set at least 4 fixing points near each rail joint. After welding the bottom of the rail, loosen the pressure plate, lower the raised part of the rail end to 20mm, and then tighten the pressure plate nut. When welding the rail waist part, gradually reduce the height of the backing plate. When the rail waist part is welded, all the backing plates should be removed and the pressing plate should be loosened. At this time, there should be a small upturn value at the rail joint.
During the head-up process, it is decided whether to tighten the pressure plate nut again according to the straightness of the rail. During the whole welding process, the deformation of the rail joint must be checked with a straight steel ruler at any time, and the height of the joint and the tightening pressure plate must be adjusted at any time to control the deformation of the rail joint. When fixing the rail joints before welding, the gap left between the two rail ends is wide at the top and narrow at the bottom. The clearance at the bottom of the rail shall prevail. It should not be less than 12mm, nor should it be too wide. Generally, it should be controlled within the range of 15-18mm.
When adjusting the fixed rail joint, in addition to ensuring the size of the end gap, the ends of the two rails must be aligned, and there must be no twisting and staggering. Before welding and during the welding process, it should be strictly checked and ensured that the position of the center lines of the two rails is on the same line, so as to prevent the bending of the rails from being bent when the welding is completed. For rails fixed with hook bolts, when welding their rail joints, temporary fixtures can be set to fix the rails according to the specific situation by referring to the above method for welding.
3. Welding
The order of welding the rail joints is from bottom to top, first the bottom of the rail, then the waist and the head of the rail, surfacing welding layer by layer, and finally repairing the surrounding area. The range of the two rail ends is 40mm each, and preheating is carried out at the same time, and the preheating and interlayer temperature are controlled at 300℃~350℃. The first layer of welding (priming): the current is 120A ~ 130A to prevent the permanent carbon steel backing plate from burning through and melting the copper backing plate, thereby reducing the difficulty of removing the red copper backing plate and shortening the track air cooling time, so as to maintain the interlayer Temperature, to prevent quenching; later layers can be used (130±15)A, each layer must be cleaned after welding to continue welding; rail waist welding: current 130 ~ 140A, welding from the lower part of the waist upwards, pay attention to slag removal .
Rail head welding: The current is 130-140A. After the copper pallet is installed, start welding. Pay attention to cleaning the slag once for each layer. Finally, perform repair welding on the unwelded parts around the weld.
4. Precautions during orbital welding
When applying the welding wave of each layer, especially when applying the welding wave of each layer at the bottom of the welding rail, one electrode should be used to finish the welding, and the arc should not be broken by connecting the electrode in the middle. The welding directions of the front and rear two layers of welding waves should be opposite. ;The welding work of each rail joint should be carried out continuously, so that the rail ends can be welded at a higher temperature (300℃~350℃). After welding, before cooling after stress relief heat treatment, it must be prevented from getting wet by rain; the hot copper plate can be removed and cooled with water, so that it can be reused next time.
5. Stress relief heat treatment (flame heating method)
The stress relief heat treatment of the rail ends after welding is an important measure to improve the welding quality. For the rails to be welded at relatively low temperatures (such as winter construction, etc.)
This measure; stress relief heat treatment is to use gas welding nozzles to repeatedly heat around the rail head, rail waist and rail bottom. The entire section of the rail should be heated as evenly as possible, and special attention should be paid to the heating quality of the rail bottom. The temperature of stress relief heat treatment is 620℃~650℃, and the range of stress relief heat treatment is 40mm on both sides from the center of the weld. The blanket is wrapped with thermal insulation cotton, and it is kept warm and cooled slowly until normal temperature.
6. Smoothing of track joints
After the rail welded joint has been stress-relieved and cooled to atmospheric temperature, the welds on the top and both sides of the rail are ground. When the welding protrusion is too large, use a grinding wheel polisher to grind it until it is flush with the rail head, and finally polish the surface.
7. Treatment of track joints at factory expansion joints
There are usually two types of rail joints at the factory expansion joints: one uses splint or fishplate connection, and the rail uses a 45° oblique joint with a gap of 10mm. The other adopts the splice plate connection processed according to the shape of the rail head, and the gap is 50mm.