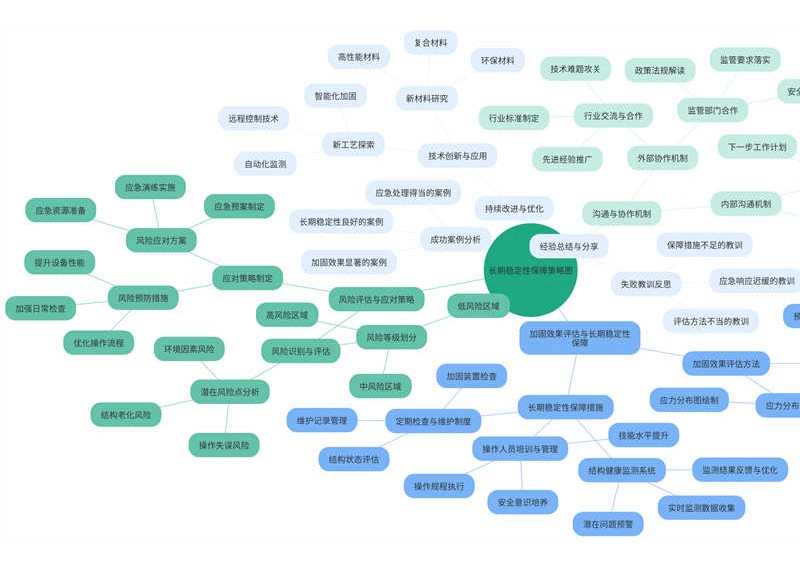
Arching and reinforcement scheme for double-girder overhead crane
As an important equipment in industrial production, the stability and safety of double girder overhead cranes are directly related to production efficiency and personnel safety. However, in the process of carrying heavy loads and frequent operation for a long time, some cranes have arching phenomenon, which not only affects the normal operation of the equipment, but also sows potential safety hazards. The emergence of arching problems is often accompanied by a decline in structural strength, so it is particularly important to find and implement effective reinforcement programs. In this paper, we will discuss the detection and analysis methods of double girder overhead travelling crane arching problems, and on this basis, we propose a set of scientific and reasonable reinforcement program, which aims to provide a strong guarantee for the smooth progress of industrial production.
Project background and crane technical parameters
In modern industrial production, double girder overhead travelling crane as a key equipment for heavy material handling, its structural stability and safety is crucial. This project analyzes and reinforces the arching phenomenon of double girder overhead travelling crane in a factory. Double girder overhead travelling crane plays a key role in industrial production due to its advantages of large span, high strength and good stability, especially in large factories, ports, yards and other scenarios where heavy materials need to be handled frequently, its efficient and safe operation is of decisive significance to maintain the stability of the production line and the efficiency of logistics.
The double girder overhead travelling crane in this project showed obvious arching phenomenon during actual operation. Arching phenomenon refers to the upward or downward bending deformation of the main girder when the crane is lifting or lowering heavy loads, which may lead to structural instability in serious cases, not only affecting the normal operation of the equipment, but also causing safety accidents. In view of this, the project team has thoroughly studied the design drawings and technical parameters of the crane, combined with the actual situation on site, and formulated a set of perfect reinforcement program aimed at improving the structural stability of the crane, eliminating potential safety hazards, and ensuring its long-term stability and efficient operation.
The main technical parameters of the crane include: span of 30 meters, lifting height of 16 meters, rated lifting capacity of 50 tons, working environment temperature range of -20 ℃ to 40 ℃, and need to withstand frequent heavy-duty operations. These parameters not only reflect the crane's strong load-bearing capacity and flexible operating range, but also its structural design, material selection and manufacturing process put forward strict requirements. However, in the actual operation process, due to the influence of various factors, such as long time high load operation, wear and tear of parts, improper maintenance, etc., resulting in the emergence of arching problems. The emergence of arching phenomenon not only affects the normal operation of the crane, but also poses a potential threat to productivity and safety. Therefore, this project aims to solve this problem by reinforcing the crane to ensure its long-term stable and efficient operation.
Crane main technical parameters table
Technical Parameters | Value/Description |
Crane Type | Double girder overhead crane |
Span | 30 meters |
Lifting height | 16 meters |
Rated lifting capacity | 50 ton |
Main application scenarios | Large factories, ports, cargo yards |
Design Features | Large span, high strength, good stability |
Frequently asked questions | Arching phenomenon (bending deformation of the main beam) |
Reinforcement purpose | Improve structural stability and eliminate safety hazards |
Crane Arching Problem Analysis and Reinforcement Solutions
Dimension of analysis | Description |
Definition of Arching | Upward or downward bending deformation of the main beam when the crane is lifting or lowering a heavy load |
Causes of arching | Prolonged high load operation, wear and tear of parts, improper maintenance, etc. |
Arching effects | Affects the normal operation of the equipment and may cause safety accidents |
Basis for the development of the reinforcement program | Design drawings, technical parameters, actual site conditions |
Reinforcement program objectives | Eliminates arching and improves structural stability |
Expected effects of reinforcement | Ensure long-term stable and efficient operation of cranes |
Detection and Analysis of Arching Problems
Detection and Measurement of Arching Problems
The discovery of the arching problem comes from the careful observation and rigorous measurement of the crane structure. With rich experience and professional knowledge, the technicians quickly captured the obvious upward bending phenomenon in the span center of the crane main girder through visual observation, which is the so-called “arching” problem. In order to accurately quantify the extent of this phenomenon, the technicians used advanced laser rangefinders and displacement sensors for accurate measurement.
During the measurement process, the technicians set up measurement points in the middle of the main girder span, 1/4 span and the end section, and recorded the displacement changes at each point under static and dynamic loads. These data clearly showed that the upward displacement of the mid-span part under the maximum working load reached 20 millimeters, far exceeding the safety standard. This finding provides strong data support for the subsequent mechanical analysis and calculation.
Mechanical Analysis and Calculation of Arching Problem
based on the detected data, the technicians carried out in-depth mechanical analysis and calculation. They found that the arching problem is mainly caused by two reasons: firstly, the crane has been subjected to heavy loads for a long time, resulting in fatigue accumulation of the metal structure; secondly, the crane has been subjected to uneven loads and vibrations in the course of use, which further aggravates the deformation of the structure.
In order to reveal the mechanical mechanism of the arching problem more intuitively, the technicians used advanced finite element analysis software to model and simulate the crane structure. By simulating the stress distribution and deformation under different working conditions, they found that the simulation results were highly consistent with the actual test results, which further verified the mechanical mechanism of the arching problem. Through these analyses and calculations, the technicians were able to more accurately predict and prevent the occurrence of the arching problem, providing a strong guarantee for the safe use of the crane.
Selection and Design of Reinforcement Options for Crane Structure Arching Problems
Overview and selection of existing reinforcement methods
In the existing reinforcement technology for crane structure arching problem, it mainly includes welding reinforcement, bolting reinforcement and prestressing reinforcement and other common programs. The advantage of welding reinforcement is its high strength, which can effectively resist the arching deformation, but this method also has obvious limitations. Welding stresses and high temperatures generated during the welding process may cause irreversible damage to the original structure, affecting the overall performance and service life of the structure. In addition, welding operations usually need to be carried out on site, making it difficult to ensure the consistency and controllability of construction quality.
Compared with welding reinforcement, the bolted reinforcement method is characterized by convenient construction and easy operation. However, this method also has certain limitations. Bolted connections may loosen during long-term use due to vibration, impact and other factors, thus affecting the reinforcement effect and the stability of the structure. In addition, the strength of bolted connections is usually lower than that of welded connections, which may make it difficult to achieve the desired reinforcement effect for large or heavy crane structures.
Considering the reinforcement effect, construction difficulty, cost and long-term stability, the project decided to adopt the prestressing reinforcement method as the main reinforcement program. By applying prestressing force inside the structure, pre-stressing reinforcement can make the structure produce anti-arch effect under the action of external force, so as to offset the arching deformation and improve the stiffness and stability of the structure. Compared with welded and bolted reinforcement, prestressing reinforcement has higher strength and stability, while the construction difficulty and cost are relatively low.
Comparison Chart of Reinforcement Methods
Improved Prestressing Tension Reinforcement Methods
The traditional pre-stressing reinforcement method, although effective, still has some limitations in practice. In order to further improve the reinforcement effect and construction efficiency, this project proposes an improved prestressed string tensioning reinforcement method. The method adopts high-strength steel strands as prestressing tendons, which have high strength and durability and can better meet the reinforcement requirements.
At the same time, adjustable tensioning devices are set at both ends of the strand to realize accurate reinforcement of the crane structure by precisely controlling the tension force and direction. The adjustable tensioning device can be adjusted according to the actual demand, making the tensioning process more flexible and accurate. In order to ensure that the reinforcement effect meets expectations, real-time monitoring of structural deformation and prestress changes during the tensioning process. Through the analysis of the monitoring data, the tensioning parameters can be adjusted in time to ensure that the structural deformation is effectively controlled.
In addition, we also adopted optimized design and construction process to further improve the reinforcement effect and construction efficiency. Through finite element analysis and other means of fine simulation and analysis of the structure, a more reasonable reinforcement scheme is formulated. A series of measures are taken during construction to minimize the interference and damage to the original structure. For example, advanced cutting and fixing techniques are used to minimize damage to the structure, and computer-aided design and robotic construction techniques are used to improve construction accuracy and efficiency.
Prestressed string reinforcement method flow
Implementation and operation of crane reinforcement program
Preparation before reinforcement
Before reinforcing the crane, a comprehensive and detailed inspection must be carried out. First of all, the structure of the crane is thoroughly inspected to ensure that the structure is intact and free from any potential safety hazards. Key components such as main beams, supporting structures and connecting parts are thoroughly inspected to make sure that there are no cracks, deformations or other defects that may affect the reinforcement effect. In order to formulate a scientific and reasonable reinforcement program, it is necessary to conduct a comprehensive and in-depth analysis based on the inspection results and the actual condition of the crane, combined with relevant design codes and standards. On this basis, the development of a targeted, practical and feasible reinforcement program. The program should elaborate the specific steps of construction, methods, precautions and expected results. Technical briefing for the construction team, so that it fully understands the specific content of the reinforcement program, mastering the reinforcement methods and operational procedures. Ensure that the construction process can be carried out in strict accordance with the requirements of the program to ensure the safety and quality of the construction process.
Installation and tensioning of reinforcement devices
In the installation process of the reinforcement device, the process requirements must be strictly followed. First of all, the anchorage and tensioning device of prestressing tendons are set in the span center part of the crane main beam. The anchorages of the prestressing tendons should be installed accurately to ensure a close fit with the main girder structure without any gap or looseness. The tensioning device should have sufficient strength and stability to effectively transmit the prestressing force. Pass the high-strength strand through the anchorage and connect it to the tensioning device. During the tensioning process, adopt a graded tensioning method to gradually increase the tensioning force. After each stage of tensioning, it should be kept for a period of time to observe the deformation of the structure and the change of prestress. The structural deformation and prestress change are monitored at the same time to ensure that the tensioning process is smooth and controllable.
Adjustment and acceptance after reinforcement
After the reinforcement is completed, the crane is fully inspected and adjusted. First, ensure that all reinforcement devices are installed correctly and the tensioning force meets the design requirements. Conduct dynamic and static load tests on the crane to verify the reinforcement effect. In the dynamic load test, simulate various load situations under actual working conditions, and observe the crane's operating status and performance indexes under dynamic conditions. The dynamic load test can assess the load carrying capacity and stability of the reinforced crane, as well as whether the working condition of each component is normal. In static load test, static load is applied to the crane to observe its deformation and stress distribution under static load. The static load test can assess whether the stiffness and strength of the reinforced crane meet the design requirements. The test results show that the displacement change in the span center of the main beam of the reinforced crane is significantly reduced, and the structural stability is significantly improved. It meets the expected target of reinforcement effect.
Reinforcement Effect evaluation and Long-term Stability Guarantee
evaluation Method of Reinforcement Effect
The assessment of reinforcement effect is mainly based on the indicators of structural deformation, stress distribution and bearing capacity. Laser range finder and stress-strain sensor are used for long-term monitoring of the reinforced crane structure. The monitoring data are regularly collected and analyzed to assess whether the reinforcement effect meets the expectation, and potential problems are detected in time. At the same time, according to the assessment results, optimize and adjust the parts that do not meet the expected effect, and re-monitor and assess until the requirements are met.
Long-term Stability Guarantee Measures
To ensure the long-term stability of the reinforcement effect, the following measures are taken:
First, a regular inspection and maintenance system is established to carry out regular inspection and maintenance of the reinforcement device to ensure that it is in good working condition. At the same time, regular inspections of the crane structure are carried out to detect and deal with potential problems in time.
Second, strengthen the training and management of crane operators, improve the skill level and safety awareness of operators, and avoid overloading and improper operation. At the same time, establish operating procedures and record systems to record and manage the operation process to ensure that the operation meets the specification requirements.
Third, establish a structural health monitoring system to monitor the status of the crane structure in real time, including structural deformation, stress distribution and bearing capacity and other indicators. Through real-time monitoring data, potential problems are found and dealt with in time to ensure the long-term stability of the reinforcement effect and the safe operation of the crane. At the same time, based on the monitoring results, the reinforcement effect is continuously evaluated and optimized and adjusted.
Long term stability assurance strategy diagram
Arching and reinforcement scheme for double-girder overhead crane